Ing. Jan Pavlík, Ph.D. |
| 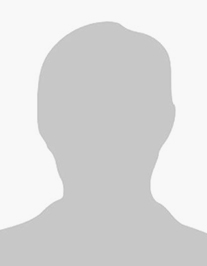 |
Education and academic qualification
- 2004, Ing., Faculty of mechanical engineering, Brno University of technology, Built production Machines
- 2011, Ph.D., Faculty of mechanical engineering, Brno University of technology, Design and Process Engineering
|
Career overview
- 2011 - today , Senior lecturer, Institute of Production Machines, Systems and Robotics, Faculty of Mechanical Engineering, Brno University of Technology
|
Scientific activities
- 2006-today High-speed Automation Handling
|
Projects
- LN00B128 - „Research Centre for Engineering Manufacturing Technique and Technology“
|
Sum of citations (without self-citations) indexed within SCOPUS
0
|
Sum of citations (without self-citations) indexed within ISI Web of Knowledge
0
|
Supervised courses:
Publications:
- PAVLÍK, J.:
PROBLEMATIC OF FAST AUTOMATIC TOOL CHANGE BY WORKING MACHINERY,
MM Science Journal, Vol.2011, (2011), No.4, pp.1-5, ISSN 1803-1269, MM publishing, s. r. o.,
journal article - other
akce: 9th International Conference Mechatronics 2011, Varšava, 21.09.2011-24.09.2011
- HOLUB, M.; OPL, M.; PAVLÍK, J.; KOLÍBAL, Z.:
DELTA - robot with parallel kinematics,
MM Science Journal, Vol.2011, (2011), No.Special Edition, pp.186-189, ISSN 1803-1269, MM publishing
journal article - other
- HOLUB, M.; PAVLÍK, J.; OPL, M.; BLECHA, P.:
IDENTIFICATION OF GEOMETRIC ERRORS OF ROTARY AXES IN MACHINE TOOLS,
Mechatronics Recent Technological and Scientific Advances, pp.213-217, ISBN 978-3-642-23243-5, (2011), Springer-Verlag Berlin Heidelberg
conference paper
akce: 9th International Conference Mechatronics 2011, Varšava, 21.09.2011-24.09.2011
- PAVLÍK, J.:
PROBLEMATIKA RYCHLÉ AUTOMATICKÉ VÝMĚNY NÁSTROJŮ U OBRÁBĚCÍCH STROJŮ, VUT v Brně
dissertation
- MATĚJKA, P.; PAVLÍK, J.; OPL, M.; KOLÍBAL, Z.; KNOFLÍČEK, R.:
Mechatronic Backlash-Free System for Planar Positioning,
Recent Advances in Mechatronics 2008-2009, pp.377-382, ISBN 978-3-642-05021-3, (2009), Springer-Verlag Berlin Heidelberg
conference paper
akce: Mechatronics 2009, Luhačovice, 18.11.2009-20.11.2009
- OPL, M.; PAVLÍK, J.; MATĚJKA, P.; KOLÍBAL, Z.:
Parallel Planar Mechanism for the Support of Education in Robotics and Mechatronics,
RAAD 2009, pp.141-141, ISBN 978-606-521-315-9, (2009), Editura Printech
conference paper
akce: 18th International Workshop on Robotics in Alpe-Adria-Danube Region (RAAD 2009), Brasov, 25.05.2009-27.05.2009
- PAVLÍK, J.; KOLÍBAL, Z.; BLECHA, P.; BLECHA, R.; BRADÁČ, F.:
Závěrečná zpráva projektu 1.2.4, VCSVTT
report
List of publications at Portal BUT
- PAVLÍK, J.:
PROBLEMATIC OF FAST AUTOMATIC TOOL CHANGE BY WORKING MACHINERY,
MM Science Journal, Vol.2011, (2011), No.4, pp.1-5, ISSN 1803-1269, MM publishing, s. r. o.,
journal article - other
akce: 9th International Conference Mechatronics 2011, Varšava, 21.09.2011-24.09.2011
The article is focused on the issue of the automatic tool change (ATC). The discussed topic can be onsidered at present to be the most relevant for the group of machines from the category of milling centres. The pressure for productivity, efficiency of the whole manufacturing process, reliability nd, last but not least, safety, leads manufacturers to design and install modern equipment for the implementation of automatic tool change which fulfil the most strict requirements. Today, the most problematic area of used equipment for ATC is the manipulator ensuring the change of the tool etween the spindle and the magazine. The kinematic arrangement and constructional solution of individual elements very significantly influence the dynamism of the whole process of change of the tool. Therefore, the work is focused just to the resolution of the issue of manipulators. The main results of the solution are the construction design of several types of manipulators, some of which were implemented within the project 1.2.4 in the Brno workplace RCMT (Research Centre of Manufacturing Technology) in the form of testing stands. Simulation models were created for selected types; for whose verification results of measurements from real equipment were used. On the basis of the solution of this issue, further key problem was identified related not only to the process of replacement, but also the complex problem of the service life of the spindle. It concerns the problem of the force originated during the process of the clamping of the tool. The article outlines possibilities for further research concerning the influences of these forces on the service life of the spindle (mainly service life of the bearing groups of the bedding of the spindle).
- HOLUB, M.; OPL, M.; PAVLÍK, J.; KOLÍBAL, Z.:
DELTA - robot with parallel kinematics,
MM Science Journal, Vol.2011, (2011), No.Special Edition, pp.186-189, ISSN 1803-1269, MM publishing
journal article - other
A complex solution of a design of the DELTA-type robot, i.e. the robot with parallel kinematics, is described in this paper. The project ensued from cooperation with the company Dyger, s.r.o., with the objective to develop a robotic device suitable for high-speed handling of small objects and applicable in many industrial configurations. The task was not only to design the mechanical part of the robot that would work together with the provided hardware and software, but also to develop our own algorithms for calculations of the target positions, singular positions of the mechanism etc.
- HOLUB, M.; PAVLÍK, J.; OPL, M.; BLECHA, P.:
IDENTIFICATION OF GEOMETRIC ERRORS OF ROTARY AXES IN MACHINE TOOLS,
Mechatronics Recent Technological and Scientific Advances, pp.213-217, ISBN 978-3-642-23243-5, (2011), Springer-Verlag Berlin Heidelberg
conference paper
akce: 9th International Conference Mechatronics 2011, Varšava, 21.09.2011-24.09.2011
Due to the ever-increasing requirements on higher productivity of ma-chines with simultaneous preservation, or even increase, of their working accuracy, considerable attention is paid to functional nodes of machines, such as linear and rotary axes. This paper describes a new concept of a universal measuring stand, developed to fulfil the requirements on monitoring of the headstock geometric properties in relation to the changing loading conditions. Equally important is the thermal stability, which can markedly affect the accuracy of the future workpiece. The problem of thermal stability of machine tools and their components is a continuously studied topic, especially the possibilities how to minimize these influences either by constructional changes or by a suitable compensation method.
For this reason, a methodology of measurement and evaluation of geometric errors of rotary axes has been proposed and, with regard to a long-term character of measurement of the heat transfer between the machine components, a universal measuring SW module has been developed.
- PAVLÍK, J.:
PROBLEMATIKA RYCHLÉ AUTOMATICKÉ VÝMĚNY NÁSTROJŮ U OBRÁBĚCÍCH STROJŮ, VUT v Brně
dissertation
This dissertation thesis is focused on the problem of the Automatic Tool Change for milling centers, which is recently shown as a very current topic. The content of this work is to conduct a comprehensive research of various types of ATC depending on the type of machine, as well as research of the current tool interface relating closely with these problems. There was made a comprehensive analysis on the basis of data obtained by comprehensive research, from which both the main factors affecting this topic and the area dealed and developed by this work resulted.
The most problematic area of machinery used nowdays for the Atomatic Tool Change was detected as manipulator provided the exchange between spindle and tool storage. Kinematic structure and design of individual elements affects very significantly the dynamics of the whole process of exchange of tools. Therefore, the work is focused on problematic of the manipulator. The main results of this thesis are constructional design of several types of manipulators, which were partly realized within the project 1.2.4 of Brno department of RCMT in the form of the testing stands. There was developed simulation models for selected types of manipulators which were verificated by measuring on the real stand.
On the basis of abovementioned problem there was identified another key issue related not only to the exchange process but also with complex problem of service life of spindle. It is a grab force in the process of picking tools. The work outlines the possibilities for further research of these forces on the service file of spindle (especially on service life of bering groups of spindle).
- PAVLÍK, J.; KOLÍBAL, Z.; BLECHA, P.; BLECHA, R.; BRADÁČ, F.; OPL, M.; NOVOTNÝ, T.:
Závěrečná zpráva projektu 1.2.4 - 2009, VCSVTT
report
The report is focused in on design of experimental stand STD-25 for testing in the field of driving units, design and control automatic tool changer.