Ing. Eva Peterková, Ph.D. |
| 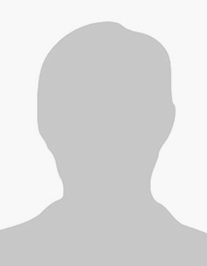 |
Education and academic qualification
- 1995, SPŠ Strojní in Prostějov, engineering specialization
- 2000, Ing., VUT FSI Brno, forming technology
|
Career overview
- 2000-till this time, doctor student FSI VUT Brno
- 2003-2004, research worker, FSI VUT Brno
- 2005-till this time, assistent, FSI VUT Brno
|
Projects
- Radial expansing problems of axially symmetric components with use elastic tool
- The tensile test analysis of thin-walled tubes
|
Supervised courses:
Publications:
- CÍSAŘOVÁ, M.; PETERKOVÁ, E.; HORÁK, M.:
Design of experimental tool for tube hydroforming, MM Science Journal
journal article in Scopus
- PETERKOVÁ, E.; SAMEK, R.:
Determination of deformation resistance in tube flaring process, MM Science Journal
journal article in Scopus
- PETERKOVÁ, E.; ŠREFL, M.:
Use of 3D measuring system ARAMIS for analysis of tube flaring process, MM Science Journal
journal article in Scopus
- PETERKOVÁ, E.:
Biaxial test of tubes using elastomer, J. E. Purkyne University in Usti n. Labem
journal article in Scopus
- PETERKOVÁ, E.; SAMEK, R.:
A New Approach to Determining the Bending Moment in Tube Forming,
Advanced Materials Research, pp.31-38, ISSN 1022-6680, Trans Tech Publications
journal article - other
- DOHNAL, I.; ŠLAIS, M.; FOREJT, M.; PETERKOVÁ, E.:
Dynamické tahové zkoušky prováděné na Hopkinsonově zařízení,
Kovárenství, Vol.2014, (2014), No.50, pp.61-64, ISSN 1213-9289, SVAZ KOVÁREN ČR o.s.
journal article - other
- PETERKOVÁ, E.; SAMEK, R.:
Stanovení ohybového momentu při tváření trubek,
Kovárenství, Vol.2014, (2014), No.50, pp.65-68, ISSN 1213-9289, SVAZ KOVÁREN ČR o.s.
journal article - other
List of publications at Portal BUT
- CÍSAŘOVÁ, M.; PETERKOVÁ, E.; HORÁK, M.:
Design of experimental tool for tube hydroforming, MM Science Journal
journal article in Scopus
When forming a material, its good formability is essential. It is primarily influence by mechanical properties and chemical composition of the material. Formability can be assessed by mechanical tests, or technological tests. Tensile test is one of the most common mechanical tests used to obtain basic mechanical properties of the material.
Another possibility how to evaluate the behavior of a material under given a load is to select a proper technological test with an appropriate experimental tool. Design of a tool should be simple, save and it should allow monitoring during the test, ie. tube hydroforming. Article deals with design of experimental tool for the realization of experiments using radial hydroforming tubes whose ends will be fixed inside the tool because of an earlier setting of limit state of deformation.
- PETERKOVÁ, E.; SAMEK, R.:
Determination of deformation resistance in tube flaring process, MM Science Journal
journal article in Scopus
The determination of the forming force required for manufacturing of the specified component is very important in practice. It is necessary to know value of the deformation resistance of the forming process for its theoretical finding. This paper presents a methodology for calculating of the total deformation resistance and subsequently of the forming force by using the theoretical equations. The method of the tube flaring was chosen for the research. The experiments were done on the testing tube samples from material 1.4301. These experiments were performed for comparing of the theoretical and real values of the forming force. The calculated values of forces differ slightly from those obtained experimentally. This difference lies in the use of the simplified input conditions and computational analysis such as material model obtained from tensile test of tubes, the chosen coefficient of friction and the simplified approach to calculation of the bending stress used in the theory of deep drawing.
- PETERKOVÁ, E.; ŠREFL, M.:
Use of 3D measuring system ARAMIS for analysis of tube flaring process, MM Science Journal
journal article in Scopus
This article analyzes the behaviour of a tube sample during the flaring process. The evaluation is carried out using non-contact 3D optical measuring system ARAMIS, which is ranked among the most modern measuring methods of deformations nowadays. The methodology of experiment including the measurement of the required values using GOM Correlate is described in this paper. The stress-strain path of an observed point was created based on the measurement values. The curves of the stress distribution and change of the wall thickness depending on the height of formed tube end were drawn too.
- PETERKOVÁ, E.:
Biaxial test of tubes using elastomer, J. E. Purkyne University in Usti n. Labem
journal article in Scopus
To obtain the values of material characteristics of tubes such as the strain hardening exponent n and the strength coefficient K is most frequently used the hydraulic bulge test. The tool and an additional equipment are often complicated and very expensive for this test. This article deals with the question whether it would be possible to obtain the corresponding values n and K by the simple biaxial test of tube using elastomer. To solve this problem, a simple tool was designed and the verification tests were realized for thin-walled tubes from material AISI 321. The results showed that it’s not possible to obtain real values n and K by biaxial test of tubes using elastomer. The reason is the elastic forming medium, which complicates the evaluation of these material characteristics, because the elastomer introduces many additional factors into the forming process.
- PETERKOVÁ, E.; SAMEK, R.:
A New Approach to Determining the Bending Moment in Tube Forming,
Advanced Materials Research, pp.31-38, ISSN 1022-6680, Trans Tech Publications
journal article - other
The article deals with more precise method of bending moment determination for rigid plastic work hardening material. Unlike earlier methods, a new methodology takes into account the real shape of the deformed tube cross-section after bending. The real centroid position of the tube cross-section, the change of the wall thickness and the irregularly deformed tube cross-section are considered. The paper presents a possible way of determining the real bending moment, reflecting the geometrical changes of the “flattened” cross-section. This approach is based on the subsequent integration of elementary bending moments, which reflects successive changes of the bending stress and a material model as well.