Ing. Aleš Prokop, Ph.D. |
| 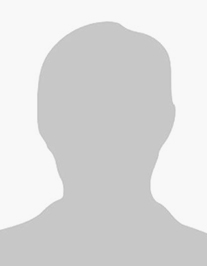 |
Education and academic qualification
- 2010, Ing., Institute of Machine and Industrial Design, Faculty of Mechanical Engineering, Brno University of Technology
- 2017, Ph.D., Institute of Automotive Engineering, Faculty of Mechanical Engineering, Brno University of Technology
|
Career overview
- 2019 - to date, Researcher, Institute of Automotive Engineering, Brno University of Technology
- 2014 - 2018, Researcher, Institute of Automotive Engineering, Brno University of Technology
- 2012 - 2014, Technician, Institute of Automotive Engineering, Brno University of Technology
- 2009 - 2012, Zetor tractors a.s. - Mechanical designer, FEM structural engineer
|
Pedagogic activities
Lectured courses:
- Semester Project (QS3)
- Vibration and Noise of Vehicles (QDZ)
- Gearing Devices of Motor Vehicles (QRU)
Supervising of the bachelor and diploma theses:
- 15 bachelor theses
- 10 diploma theses
Supervisor specialist of 2 students dostoral study
|
Academic internships abroad
- 04/2022 - 06/2022, LUT University, Finland, work internship
- 10/2018 - 11/2018, Technische universität Dresden, Germany, work internship
- 06/2012 - 12/2012, Tampere University of Technology, Finland, work internship, project Kämiko (TEKES)
- 01/2012 - 06/2012, Tampere University of Technology, Finland, study internship
|
Projects
-
2018-2021, Specific long-life couplings for rail vehicle transmission, project TAČR Epsilon TH03010183, co-researcher
-
2017-2019, Very High Speed Train Transmission, project TAČR Epsilon TH02010725, co-researcher
-
2014-2017, Research and development of powertrains with modern accumulative injection systems to minimize the harmful substances in exhaust gases, projekt TAČR Alfa TA04030454, member of the research team
-
2013-2015, Full reverse double flow gearbox with automated electro-hydraulic shifting, Project TA03011378, member of the research team
-
2011-2014, Research and development of powertrain with progressive members for decrease of harmful substances in exhaust gasses, project MPO FR-TI3/207
-
2011-2013, Research of suitable methods for decrease of powertrain vibrations, Project FS-S-11-8
- 2009-2012, Research and Development of Two Stroke CI Engine with Opposite Pistons, Project FR-TI1/580, Ministry of Industry and Trade
|
Sum of citations (without self-citations) indexed within SCOPUS
3
|
Sum of citations (without self-citations) indexed within ISI Web of Knowledge
1
|
Supervised courses:
Publications:
- JANOUŠEK, M.; PROKOP, A.; NOVOTNÝ, P.:
Locating of the Noise Sources in Automotive Industry,
Proceedings of the XLIV. International Scientific Conference of the Czech and Slovak University Departments and Institutions Dealing with the Research of Internal Combustion Engines, pp.133-140, ISBN 978-80-7375-801-1, (2013), Mendelova univerzita v Brně
conference paper
akce: XLIV. International Scientific Conference of the Czech and Slovak University Departments and Institutions Dealing with the Research of Internal Combustion Engines, Brno, 10.09.2013-11.09.2013
- PROKOP, A.:
Inverse Monitoring of Loading State with Output Measurements,
International Journal of COMADEM, Vol.16, (2013), No.2, pp.54-59, ISSN 1363-7681
journal article - other
- NOVOTNÝ, P.; PÍŠTĚK, V.; DRÁPAL, L.; PROKOP, A.:
Simulation Approaches for the Solution of Cranktrain Vibrations,
MECCA - Journal of Middle European Costruction and Design of Cars, Vol.2012, (2012), No.4, pp.34-43, ISSN 1214-0821, ČVUT v Praze
journal article - other
- AMBRÓZ, R.; PÍŠTĚK, V.; NOVOTNÝ, P.; PROKOP, A.:
Simulation and Experimental Tools For Powertrain Noise Reduction,
Technológ, Vol.2011, (2011), No.3, pp.28-36, ISSN 1337-8996, TU v Žilině
journal article - other
List of publications at Portal BUT
- ZUBÍK, M.; NOVOTNÝ, P.; PROKOP, A.; JANOUŠEK, M.:
Virtual Powertrain – a Tool for NVH Improvement,
Setkání uživatelů MSC.SOFTWARE 2014, pp.95-100, ISBN 978-80-260-6033-8, (2014), MSC.Software s.r.o.
conference paper
akce: Setkání uživatelů MSC.SOFTWARE 2014, Brno, 11.06.2014-12.06.2014
This paper presents a computational approach for further visualization of powertrain sound based on number of cylinders or other parameters respectively. The Virtual Engine as an advanced computational model using MSC.ADAMS software together with the MATLAB post processing is used for all computations. Brief introduction about development and basic principles of the models are also presented.
- JANOUŠEK, M.; PROKOP, A.; NOVOTNÝ, P.:
Locating of the Noise Sources in Automotive Industry,
Proceedings of the XLIV. International Scientific Conference of the Czech and Slovak University Departments and Institutions Dealing with the Research of Internal Combustion Engines, pp.133-140, ISBN 978-80-7375-801-1, (2013), Mendelova univerzita v Brně
conference paper
akce: XLIV. International Scientific Conference of the Czech and Slovak University Departments and Institutions Dealing with the Research of Internal Combustion Engines, Brno, 10.09.2013-11.09.2013
Vehicle noise is very actual topic today because there are very strict regulations given by EU. Noise on vehicle is produced by different subsystems of the vehicle and goal is optimize each of them to reduce overall acoustic emission. Locating noise sources of each subsystem is very important, because it helps to understand acoustic behavior of structure. Noise source localization can help in future research and development. Furthermore is really important to be able to locate noise sources with reliable and precise method. Acoustic Camera is one of the modern methods how to locate noise sources, the main idea is see what you hear. This article is about Acoustic camera application on the real noise location problems in automotive industry.
- PROKOP, A.:
Inverse Monitoring of Loading State with Output Measurements,
International Journal of COMADEM, Vol.16, (2013), No.2, pp.54-59, ISSN 1363-7681
journal article - other
In many industrial cases it is difficult or very often even impossible to measure directly loading forces acting on the structure. In this kind of situations one possibility is to apply inverse monitoring principle. This means computation methods for determining forces from the output that the forces generate. This paper presents an application of the use of inverse computation
method applied for determining the magnitude and location of loading forces on a structure. For the inverse computation presented method utilizes an influence coefficient approach. In this principle an influence coefficient matrix (ICM) that describes the relation between external loading forces and measured strains in the structure is used (Doyle). The elements of the matrix are in this case obtained from finite element (FE) model of the structure. One problem in the use of the inverse method is that it is very often ill-posed. In practice this means that small errors in strain measurement results can cause large errors in force computation and also difficulties in matrix computation which is used in the method. The method is applied on a loaded cantilever beam that is rigidly connected with a welded structure. Validation of presented method is conducted by comparing its results with measured values of an experiment. The effect of error in the measured data on the accuracy of the inverse calculation is a crucial problem and it is discussed as well. The method shows promising results and proves that it is robust enough for industrial application.
- NOVOTNÝ, P.; PÍŠTĚK, V.; DRÁPAL, L.; PROKOP, A.:
Simulation Approaches for the Solution of Cranktrain Vibrations,
MECCA - Journal of Middle European Costruction and Design of Cars, Vol.2012, (2012), No.4, pp.34-43, ISSN 1214-0821, ČVUT v Praze
journal article - other
A development of modern powertrains requires an incorporation of advanced CAE tools enabling to decrease desired engine development times and costs. Modern computational models become more and more complicated and enable to integrate many physical problems. Concentrating on powertrain dynamics and component fatigue, a few basic approaches can be used for solution. The first approach incorporates a separate dynamics solution of the powertrain parts. The second one solves a complete powertrain model including all significant parts like a cranktrain, a valvetrain, a gear timing drive or an injection pump. The paper deals with dynamics and fatigue analyses solved by different approached. Computed and measured results originate from the tractor compression-ignition in-line six-cylinder engine.
- AMBRÓZ, R.; PÍŠTĚK, V.; NOVOTNÝ, P.; PROKOP, A.:
Simulation and Experimental Tools For Powertrain Noise Reduction,
Technológ, Vol.2011, (2011), No.3, pp.28-36, ISSN 1337-8996, TU v Žilině
journal article - other
The automotive industry has constantly been pursuing ways to reduce the vehicle noise and vibrations in response to the ever-increasing customer demand on comfort and government regulation on noise emission. The first stage of the noise prediction procedure is made to quantify noise levels for different design concepts and has to be available in time for the concept design decision. Due to shorten design phases it is nowadays necessary to evaluate the acoustic behaviour in the design phase based on CAEA data.