Ing. Kamil Řehák, Ph.D. |
| 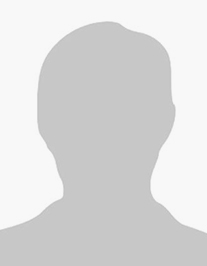 |
Sum of citations (without self-citations) indexed within SCOPUS
H-index = 3
|
Sum of citations (without self-citations) indexed within ISI Web of Knowledge
2
|
Supervised courses:
Publications:
- MARCIÁN, P.; KONEČNÝ, O.; BORÁK, L.; VALÁŠEK, J.; ŘEHÁK, K.; KRPALEK, D.; FLORIAN, Z.:
On the Level of Computational Models in Biomechanics Depending on Gained Data from Ct/Mri and Micro-Ct,
MENDEL 2011 - 17th International Conference on Soft Computing, pp.255-267, ISBN 978-80-214-4302-0, (2011), Brno University of Technology
conference paper
akce: 17th International Conference of Soft Computing, MENDEL 2011, Brno University of Technology, 15.06.2011-17.06.2011
- MATUG, M.; VAŠEK, M.; MIŠUN, V.; NAVRÁTIL, P.; CIVÍN, A.; ŘEHÁK, K.:
Analysis of influence of vocal fold - vocal tract models connection by using FEM,
Engineering Mechanics 2011, 17th International Conference, pp.391-394, ISBN 978-80-87012-33-8, (2011), Institute of Thermomechanics
conference paper
akce: Engineering Mechanics 2011, Svratka, 09.05.2011-12.05.2011
- MARCIÁN, P.; BORÁK, L.; VALÁŠEK, J.; KRPALEK, D.; ŘEHÁK, K.; NAVRÁTIL, P.:
Creation of Computational Models of Cancellous Bone,
Engineering Mechanics 2011, 17th International Conference, pp.379-382, ISBN 978-80-87012-33-8, (2011), Institute of Thermomechanics
conference paper
akce: Engineering Mechanics 2011, Svratka, 09.05.2011-12.05.2011
- ŘEHÁK, K.; FLORIAN, Z.; KRPALEK, D.; MARCIÁN, P.; MATUG, M.; VALÁŠEK, J.:
Stress analysis of Burch-Schneider cage,
Engineering Mechanics 2011, 17th International Conference, pp.523-526, ISBN 978-80-87012-33-8, (2011), Institute of Thermomechanics
conference paper
akce: Engineering Mechanics 2011, Svratka, 09.05.2011-12.05.2011
- VALÁŠEK, J.; MARCIÁN, P.; KRPALEK, D.; ŘEHÁK, K.; MANEK, F.; FLORIAN, Z.:
Stress Strain Analysis Of Restored First Molar With Cavity Of Class I.,
Engineering Mechanics 2011, 17th International Conference, pp.635-638, ISBN 978-80-87012-33-8, (2011), Institute of Thermomechanics
conference paper
akce: Engineering Mechanics 2011, Svratka, 09.05.2011-12.05.2011
List of publications at Portal BUT
- ŘEHÁK, K.; PROKOP, A.; ZAJAC, R.; OTIPKA, V.:
Acoustic and Vibration Response Analysis of Heavy-Duty Gearbox,
Acoustics and Vibration of Mechanical Structures—AVMS 2019, pp.443-451, ISBN 978-3-030-54135-4, (2019), Springer Science and Business Media Deutschland GmbH
conference paper
akce: ACOUSTICS AND VIBRATION OF MECHANICAL STRUCTURES, Temešvár, 30.05.2019-31.05.2019
The presented paper deals with determination of acoustic and vibration response of heavy-duty gearbox housing on the defined force excitation. The analysis is performed by both, numerical and experimental approach. The results from both approaches are compared to validate numerical approach for the pur-pose to use numerical model for design optimization and further for multi-body simulations. The excitation is applied to the area of bearing to simulate the real character of the excitation, which is transmitted from the gear mesh contact stiff-ness, which is changing due to actual geometry of teeth in contact, via gears and shafts to bearings and further to the housing. The same boundary conditions are applied for both approaches. Because the vibrations and the acoustic emissions are directly related to each other, the surface normal acceleration in critical loca-tions are compared first. When the surface normal acceleration is compared, the sound pressure level in defined locations is evaluated. This article systematically describes the prediction of vibro-acoustics behaviour of heavy-duty gearbox housing by using two different levels of approach, which can be used for design optimization afterwards. The technical experiment with optimized housing has not been performed yet.
- PROKOP, A.; ŘEHÁK, K.; ZAJAC, R.; OTIPKA, V.:
Gear Shift Investigation Using Virtual Prototype,
Acoustics and Vibration of Mechanical Structures—AVMS 2019, pp.415-424, ISBN 978-3-030-54135-4, (2019), Springer Science and Business Media Deutschland GmbH
conference paper
akce: ACOUSTICS AND VIBRATION OF MECHANICAL STRUCTURES, Temešvár, 30.05.2019-31.05.2019
The presented paper deals with prediction of vibro-acoustic behavior of heavy-duty transmission concept by application of virtual prototype. The methodology was developed by combination of both, numerical and experi-mental approach on single stage gearbox. The results from both approaches were compared to validate computational simulation for the purpose to use numerical model for assembly with higher level of complexity. The whole methodology is applied on heavy-duty transmission concept. For the purpose of easy application to different gearbox concept, the more complex model is written as open code. This enables to include gear shift option tuning, which can significantly affect vehicle comfort. This paper is mainly focused on the investigation of different gear shift process influence on the surface normal velocity which is evaluated on the gearbox housing and is related to the acoustic behaviour. The different com-bination of clutch activation and deactivation profile at different torque is inves-tigated and evaluated by surface normal velocity at most sensitive locations. Based on the results, the multibody model can be used at designing and optimi-zation phase from the vibro-acoustic point of view.
- ŘEHÁK, K.; KUČERA, P.; PROKOP, A.:
Application of Virtual Prototype to Heavy-duty Gearbox housing evaluation,
TRANSBALTICA XI: Transportation Science and Technology, pp.361-368, ISBN 978-3-030-38665-8, (2019), Springer International Publishing
conference paper
akce: International Conference TRANSBALTICA 2019, Vilnius, 02.05.2019-03.05.2019
This paper deals with application of methodology for design of gear-box and its validation by technical experiment. First, the methodology for gearbox was developed and validated on the small single-stage gearbox concept, which ena-bles simple modifiability. The methodology can be divided into three different level (modal analysis, harmonic analysis and multibody simulation). The outputs from pre-vious model increase accuracy of next level of model. Each step of methodology was validated by partial experiment. The sensitivity of input parameters is investigated afterwards to see the limits of methodology. The methodology is applied on a heavy-duty gearbox concept afterward, where all inputs parameters are calculated in similar way as in case of small single-stage gearbox. A partial experimental approach to val-idate the application of virtual prototype on very complex and extremely loaded com-ponent were performed. Based on the results from numerical approach and their com-parison to the measurement, the virtual prototype is powerful tool, which can be used in designing phase or in case of optimization.
- ŘEHÁK, K.; KOPEČKOVÁ, B.; PROKOP, A.:
Dynamic Analysis of Single Stage Gearbox with Backlash Influence,
Transport Means 2017, pp.575-579, (2017)
conference paper
akce: Transport Means 2017, Juodkranté, 20.09.2017-22.09.2017
The helical gear is the most used type of gears in automotive. The understanding of the gears dynamic behaviour is key
to improve design with goal of decrease vibration and emitted noise. For that purpose, the dynamic modelling approach
based on the finite element method and multi-body dynamic software approach on single stage gearbox is proposed. After
validation of numerical approach by experimental measurement, the backlash influence on dynamic behaviour is
investigated.
- PROKOP, A.; ŘEHÁK, K.:
VIRTUAL PROTOTYPE APPLICATION TO HEAVY-DUTY VEHICLE GEARBOX CONCEPT ,
Engineering Mechanics 2017, pp.810-813, ISBN 978-80-214-5497-2, (2017)
conference paper
akce: ENGINEERING MECHANICS 2017, Svratka, 15.05.2017-18.05.2017
This paper deals with application of virtual prototype to the heavy-duty vehicle gearbox concept.
First the methodology is developed and tested on the single-stage gearbox concept, where the sensitivity of
input parameters is investigated and validated by the experiment. The methodology is applied to the heavy-duty vehicle gearbox concept, where all inputs parameters are calculated similarly as in case of single-stage gearbox. The virtual prototypes enable to investigate influence of different input parameters on the design parameters, which are necessary at design phase. The surface normal velocity, which is related to noise prediction, can be evaluated. An experimental approach to validate the application on such high level of gearbox has not been performed yet.