Ing. Ondřej Andrš, Ph.D. |
| 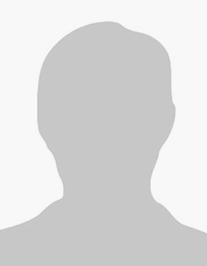 |
Education and academic qualification
2007, Ing, Fakulta strojního inženýrství VUT v Brně, obor Inženýrská informatika a automatizace
|
Pedagogic activities
Bakalářské studium: inteligentní řídicí systémy, automatizace
|
Scientific activities
- Controllers based on soft-computing
- Movement control of technical systems, mechatronics
|
Sum of citations (without self-citations) indexed within SCOPUS
16
|
Publications:
- ANDRŠ, O.; VETIŠKA, J.; HOLUB, M.; KOVÁŘ, J.:
Model Based Design of Fuel Pump Control,
Applied Mechanics and Materials, Vol.2016, (2016), No.821, pp.601-607, ISSN 1662-7482, Trans Tech Publications
journal article - other
- RUČKA, J.; KOVÁŘ, J.; ANDRŠ, O.; SUCHÁČEK, T.:
Aspects of pressure sewerage system design, MM Science Journal
journal article in Scopus
- ANDRŠ, O.; HADAŠ, Z.; KOVÁŘ, J.; VETIŠKA, J.; SINGULE, V.:
Model-Based Design of Mobile Platform with Integrated Actuator – Design with Respect to Mechatronic Education,
MECHATRONICS 2013: RECENT TECHNOLOGICAL AND SCIENTIFIC ADVANCES, pp.891-988, ISBN 978-3-319-02294-9, (2013), Springer
conference paper
akce: 10th International Conference on Mechatronics, Brno, 07.10.2013-09.10.2013
- ANDRŠ, O.; KOVÁŘ, J.:
FORWARD KINEMATICS MODELLING OF A PARALLEL DEVICE FOR CORD IMPLANTS TUNING,
19th International Conference on Soft Computing MENDEL 2013, pp.283-288, ISBN 978-80-214-4755-4, (2013)
conference paper
akce: 19th International Conference on Soft Computing, MENDEL 2013, Brno University of Technology, 26.06.2013-28.06.2013
- HADAŠ, Z.; VETIŠKA, V.; SINGULE, V.; ANDRŠ, O.; KOVÁŘ, J.; VETIŠKA, J.:
Energy Harvesting from Mechanical Shocks Using A Sensitive Vibration Energy Harvester,
International Journal of Advanced Robotic Systems, Vol.2012, (2012), No.9, pp.1-7, ISSN 1729-8806, InTech Europe
journal article - other
- KOVÁŘ, J.; ANDRŠ, O.; BŘEZINA, L.; SINGULE, V.:
Laboratory Delta Robot For Mechatronic Education Purposes,
Proceedings of International Symposium on Power Electronics, Electrical Drives, Automation and Motion - SPEEDAM 2012, pp.1209-1212, ISBN 978-1-4673-1299-8, (2012)
conference paper
akce: International Symposium On Power Electronics, Electrical Drives, Automation and Motion - SPEEDAM 2012, Sorrento, 20.06.2012-22.06.2012
- BŘEZINA, T.; ANDRŠ, O.; HOUŠKA, P.; BŘEZINA, L.:
Some notes to the design and implementation of the device for cord implants tuning,
Recent advances in Mechatronics 2008 - 2009, pp.335-340, ISBN 978-3-642-05021-3, (2009), Springer-Verlag Berlin Heidelberg
conference paper
akce: Mechatronics 2009, Luhačovice, 18.11.2009-20.11.2009
List of publications at Portal BUT
- ANDRŠ, O.; VETIŠKA, J.; HOLUB, M.; KOVÁŘ, J.:
Model Based Design of Fuel Pump Control,
Engineering Mechanics 2015 Extended Abstracts, pp.10-11, ISBN 978-80-86246-42-0, (2015), Institute of Theoretical and Applied Mechanics, Academy of Sciences of the Czech Republic
conference paper
akce: Engineering Mechanics 2015, Svratka, 11.05.2015-14.05.2015
This paper presents a co-simulation method to design of speed controller for turbojet fuel pump. Expected fuel pump is used for small turbine engine concept with reducer driven by free turbine. The amount of injected fuel into the combustion chamber is based on the speed of the fuel pump which is controlled by the engine control unit. The final flow of fuel into the combustion chamber is restricted by fuel bypass which constricts the return fuel according to pressure in the nozzles. This back fuel bypass has nonlinear and fixed characteristic determined by its structure. The only way how to control the amount of incoming fuel to the engine is the pump speed control. Effect of the bypass represents a variable component in the fuel pump load and from the view of the speed controller it is a disturbance variable. This paper describes the co-simulation model based on the use of MATLAB/Simulink and MSC Adams environment. This simulation uses interconnection of Simulink controller design and simplified model of the fuel pump dynamics in Adams (without hydraulic modeling).
- ANDRŠ, O.; KOVÁŘ, J.; HADAŠ, Z.:
Introduction to Design of Speed Controller for Fuel Pump,
Proceedings of the 16th International Conference on Mechatronics – Mechatronika 2014, pp.672-676, ISBN 978-80-214-4817-9, (2014), VUT v Brně
conference paper
akce: 16th International Conference on Mechatronics - Mechatronika 2014, Brno, 03.12.2014-05.12.2014
This contribution presents an efficient approach to
design of speed controller for fuel pump. The fuel pump is used
for two-shaft turbine engine concept with reducer driven by a
free turbine. Controlling the amount of fuel injection into the
combustion chamber is based on the speed control of the fuel
pump which is controlled by the engine control unit according to
the desired power mode. The resulting flow of fuel into the
combustion chamber beside the pump speed regulator influences
the bypass which constricts the return fuel according to pressure
in the nozzles. Control characteristic of the bypass controller is
fixed and is determined by its structure. The only adjustable
parameter is the speed of the fuel pump. This paper describes the
design procedure of this fuel pump using a two-level controller
with speed and subordinate current-torque control.
- HADAŠ, Z.; ANDRŠ, O.; VETIŠKA, V.; ANČÍK, Z.:
ENERGY HARVESTING TECHNOLOGIES FOR SPECIAL APPLICATIONS,
Proceedings of the International Conference on Military Technologies 2013 (ICMT'13), pp.173-181, ISBN 978-80-7231-917-6, (2013), University of Defence
conference paper
akce: ICMT'2013 - INTERNATIONAL CONFERENCE ON MILITARY TECHNOLOGIES 2013, Brno, 22.05.2013-23.05.2013
This paper deals with review and assessment of energy harvesting technologies applicable to special applications. These technologies harvest electrical energy from their surroundings using several physical principles. Surrounding of each technical system is enclosed by several types of ambient energy and this energy can be used for autonomous feeding of electrical devices. We can assume harvesting from mechanical energy of movement, vibration and shocks, solar and thermal energy, etc. Generally the amount of harvested energy is in very low level. However, a power consumption of modern electronic devices is in very low level too. Therefore these technologies can be very useful for autonomous supplying of many applications, for example autonomous electronics and diagnostic systems, wire-less sensors, wireless communications, etc. The autonomous energy harvesting sources will be described in this paper and the applicability for special applications will be evaluated.
- BŘEZINA, T.; ANDRŠ, O.; BŘEZINA, L.; HADAŠ, Z.; HOUŠKA, P.; KOVÁŘ, J.; VETIŠKA, J.:
VIRTUAL DESIGN OF INDUSTRIAL MANIPULATOR USING MECHATRONIC APPROACH,
Proceedings of the International Conference on Advances in Mechatronics 2011 (AIM 11), pp.105-110, ISBN 978-80-7231-848-3, (2011), Expertia o.p.s.
conference paper
akce: Advances in Mechatronics 2011, Brno, 07.12.2011-09.12.2011
This paper deals with a simulation modelling of an industrial manipulator, which is modelled as mechatronic system. This manipulator model consists of rigid parts, DC motors, control system and sensors. The manipulator parts and joints create multi-body system, which is driven by DC motors. The correct positioning of manipulator effector is provided by control system of DC motors. The mechatronic approach of a model-based design is used for this industrial task. The multi-body model of the manipulator in Adams is controlled by the control model in Simulink environment. This co-simulation technique is used for the design and optimization analysis of the industrial manipulator. The co-simulation model can be used for an optimal design of manipulator parameters and dynamic analysis of this mechatronic system.
- ANDRŠ, O.; BŘEZINA, T.; KOVÁŘ, J.:
Design of fuzzy logic controller for DC motor,
Mechatronics Recent Technological and Scientific Advances, pp.9-18, ISBN 978-3-642-23243-5, (2011), Springer
conference paper
akce: 9th International Conference Mechatronics 2011, Varšava, 21.09.2011-24.09.2011
This contribution presents a simple and efficient approach to the fuzzy logic controller design and simulation. The proposed controller uses a Sugeno type fuzzy inference system (FIS) which is derived from discrete position state-space controller with an input integrator. The controller design meth-od is based on anfis (adaptive neuro-fuzzy inference system) training rou-tine. It utilizes a combination of the least-squares method and the back-propagation gradient descent method for training FIS membership function parameters to emulate a given training data set. The proposed fuzzy logic controller is used for the position control of a linear actuator which is a part of a Stewart platform.