Ing. Jan Řiháček, Ph.D. |
| 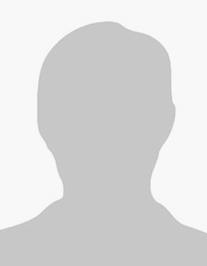 |
Supervised courses:
Publications:
- ŘIHÁČEK, J.; MRŇA, L.:
Comparison of Implicit and Explicit Algorithms of Finite Element Method for the Numerical Simulation of Hydroforming Process, MM Science Journal
journal article in Scopus
- VANĚK, M.; ŘIHÁČEK, J.; MORAVEC, J.:
Improvement of Model of Aluminium Alloys Behaviour for Application in Numerical Simulations of Welding, MM Science Journal
journal article in Scopus
- LIDMILA, Z.; PODANÝ, K.; ŘIHÁČEK, J.:
Improving of shearing blades life, MM Science Journal
journal article in Scopus
- PODANÝ, K.; LIDMILA, Z.; ŘIHÁČEK, J.:
Proposal of the flexible tool for the production of aerospace parts, MM Science Journal
journal article in Scopus
- ŘIHÁČEK, J.; MRŇA, L.:
Forming a Structured Surface of a New Type of Solar Absorber with Hydroforming,
Advanced Materials Research, pp.49-54, ISSN 1022-6680, Trans Tech Publications
journal article - other
- ŘIHÁČEK, J.; VANĚK, M.:
Možnosti zkvalitnění sítě MKP při simulacích objemového tváření v software ANSYS Workbench 16
,
Kovárenství, pp.9-12, ISSN 1213-9289, Svaz kováren České republiky
journal article - other
- ŘIHÁČEK, J.; MRŇA, L.:
Optimization of Hydroforming Die Geometry For Manufacturing of Solar Absorbers,
METAL 2015, pp.1-6, ISBN 978-80-87294-58-1, (2015)
conference paper
akce: METAL 2015 24th International Conference on Metallurgy and Materials, Brno, 03.06.2015-05.06.2015
List of publications at Portal BUT
- ŘIHÁČEK, J.; MRŇA, L.:
Comparison of Implicit and Explicit Algorithms of Finite Element Method for the Numerical Simulation of Hydroforming Process, MM Science Journal
journal article in Scopus
This paper deals with numerical simulation possibilities of a hydroforming technology in production of a flow solar absorber with structured surface in a single technological operation. An austenitic stainless steel X5CrNi18-10 is used as a material for the production of the flow solar absorbers. In the theoretical chapters, comparison between implicit and explicit algorithms of finite element method (FEM) is performed. Experimental part of the paper includes creation of geometrical, material and computational models for the explicit and the implicit solution in software ANSYS Workbench and ANSYS LS-DYNA. Finally, due to evaluation of the experiment and FEM results, comparison between the implicit and the explicit theoretical solution of a formed part thickness is performed.
- VANĚK, M.; ŘIHÁČEK, J.; MORAVEC, J.:
Improvement of Model of Aluminium Alloys Behaviour for Application in Numerical Simulations of Welding, MM Science Journal
journal article in Scopus
This article describes how to modify numerical solutions to enable more accurate prediction of the size of heat affected zones (HAZ) during welding of heat treatable aluminium alloys. The size of HAZ affects properties of a weld joint, such as e.g. hardness and strength, and it is also a factor on residual stress and deformation after welding depends.
Welding experiments were performed using material EN AW-6082 to obtain input data for numerical simulations. Calibration thermo-metallurgical numerical analyses were performed using simulation software Sysweld, where data from the standard Sysweld material database were used. Subsequently, based on information from literature and data obtained during welding experiments, some changes of parameters in Leblonds formula (which describes metallurgical transformation in HAZ) were done.
The results obtained with modified material database show that it is possible to perform numerical simulations of aluminium welding with significantly more accurate prediction of the size of the HAZ.
- LIDMILA, Z.; PODANÝ, K.; ŘIHÁČEK, J.:
Improving of shearing blades life, MM Science Journal
journal article in Scopus
In the paper, design and implementation of a method for increase of shearing blades life are described. Blades for shearing of a reinforcing grip bar are made of tool steel 55WCrV8 (19 733 according to Czech Standard). Plasma nitriding method, which allows higher surface hardness while maintaining a ductile core, was chosen as an optimal method increasing blades life. A scratch pattern and a hardness measurement of initial and modified samples confirmed improvement in blade surface hardness to a value of 64 HRC.
- PODANÝ, K.; LIDMILA, Z.; ŘIHÁČEK, J.:
Proposal of the flexible tool for the production of aerospace parts, MM Science Journal
journal article in Scopus
The paper is focused on the design of a container tool for forming of sheet metal parts used in the aerospace industry, which is based on a flexible medium. The tool is intended for hydraulic press CBJ 500-6 and it is multi-purpose for a wide range of materials, shapes and sizes. A combination of polyurethane plates Fibroflex and two rubber plates are used as an elastic medium. A punch is made of plywood of 28 mm thick with negative shape of a part. For elimination of a springback during a bending operation, relieving of bending surfaces is performed. The designed tool and its dimensions are verified by using FEM analysis and subsequently also by practical experiment, i.e. verification and debugging functionality for a standard product of aluminium alloy 6061.T6.
- ŘIHÁČEK, J.; MRŇA, L.:
Forming a Structured Surface of a New Type of Solar Absorber with Hydroforming,
Advanced Materials Research, pp.49-54, ISSN 1022-6680, Trans Tech Publications
journal article - other
One of the ways to increase efficiency of the solar absorber is modification of absorption area in the system of pyramidal cavities, where the incident radiation is absorbed by multiple reflections. The paper deals with the technology of production of the flow solar absorber with a structured surface in a single technological operation using hydroforming. Two laser-welded sheets are inserted into the forming chamber. Then the space between them is pressurized with hydraulic fluid which causes their form to the desired shape. The first part of this article describes hydroforming device. The second section deals with theoretical simulation of forming a different structured surface in the programming environment of ANSYS. As follows practical test of hydroforming is performed. Austenitic stainless steel X5CrNi18-10 was used as a material for the production of samples.