doc. Ing. Pavel Mazal, CSc. |
| 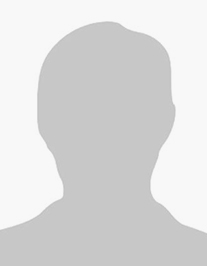 |
Education and academic qualification
- 1979, Ing., Faculty of Mechanical Engineering BUT in Brno
- 1985, CSc., CSAV IPM Brno
- 2004, Assoc.Prof., FME BUT in Brno
|
Career overview
- 1980-1984, Czechoslovak Academy of Sciences, IPM Brno
- 1985-1991, lecturer, BUT in Brno, FME, Department of Machine Parts
- 1991-1993, lecturer, ENSET, Université de Tunis
- 1994- vice director, Institute of Machine Design, FME BUT in Brno
- 2004- Assoc.Prof, Institute of Machine Design, FME BUT in Brno
|
Scientific activities
- Fatigue properties of materials and constructions.
- Application of acoustic emission method.
|
Non-University activities
- since 2000, President of the Czech Society for NDT
- since 2000, member of General Assembly of European Federation of NDT
- since 2000, member of Editor. Board of Journal of Acoustic Emission (USA)
- since 2002, member of Editor. Board of NDT Welding Bulletin (ČR)
- since 2005 , member of Editor. Board of Int.Jour. of Microstructure and Materials properties (UK)
|
Keywords
- fatigue of materials
- contact fatigue
- nondestructive testing
- bearings
|
Projects
- Application of selected NDT methods at continuous damage degree evaluation of cyclically loaded - GACR 106/02/0745, Grant agency of CR, 2002 – 2004.
- Bainitic steel for dynamically loaded components - GACR 106/02/1319, Grant agency of CR, 2002 – 2004.
- Research of contact damage phases using the method of acoustic emission - GACR 106/06/0343, Grant agency of CR, 2006 – 2008.
- Research of new methods of measurements and evaluation of acoustic emission signal - project of MPO (Impuls), 2006 - 2008.
- Detection and Identification of the development of cyclic damage of modern AlMg alloys with the application of specific NDT procedures- Grant agency of CR 2007-2009.
- Integrated system of continual monitoring of selected machine parts and technologies with application of the acoustic emission. Project MPO ČR - TIP, 2009-2012.
|
Supervised courses:
Publications:
- VLAŠIC, F.; VOLÁK, J.; NOHÁL, L.; MAZAL, P.; HORT, F.:
Study of Initial Stages of Fatigue Process Using Non-destructive Testing Methods, Trans Tech Publications
journal article in Web of Science
akce: Materials Structure & Micromechanics of Fracture (MSMF-7), Brno, 01.07.2013-03.07.2013
- NOHÁL, L.; HORT, F.; DVOŘÁČEK, J.; MAZAL, P.:
An Experimental Investigation of Rolling Contact Fatigue of Steels Using Acoustic Emission Method,
INSIGHT, Vol.55, (2013), No.12, pp.665-669, ISSN 1354-2575, BINDT
journal article - other
- MAZAL, P.; PAZDERA, L.; NOHÁL, L.; TOPOLÁŘ, L.:
Netradiční aplikace metody akustické emise,
ISBN 978-80-214-4629-8, (2012), VUT v Brně
book
- MAZAL, P.; HORT, F.; VLAŠIC, F.:
Acoustic Emission Diagnostics of Roller Bearings Damage,
Nondestructive Testing of Materials and Structures, pp.411-418, ISBN 978-94-007-0722-1, (2012), Springer
book chapter
akce: Nondestructive Testing of Materials and Structures, Istanbul, 15.05.2011-18.05.2011
- MAZAL, P.; LIŠKUTÍN, P.; VLAŠIC, F.; HORT, F.:
Usage of Acoustic Emission Signal and X-ray Diffraction Analysis for Detection of Microstructural Changes in Cyclically Loaded AlMg Alloys,
Nondestructive Testing of Materials and Structures, pp.319-326, ISBN 978-94-007-0722-1, (2012), Springer
book chapter
akce: Nondestructive Testing of Materials and Structures, Istanbul, 15.05.2011-18.05.2011
- HORT, F.; MAZAL, P.; VLAŠIC, F.:
Monitoring of Acoustic Emission Signal of Loaded Axial Bearings,
Journal of Materials Science and Engineering A, Vol.2011, (2011), No.5A, pp.717-724, ISSN 1934-8959, David Publishing
journal article - other
- MAZAL, P.; PAZDERA, L.; NOHÁL, L.; TOPOLÁŘ, L.; GRUM, J.:
ACOUSTIC EMISSION IN QUALITY CONTROL OF MATERIALS AND PROCESSES MONITORING,
ISBN 978-961-90610-8-4, (2011), University of Ljubljana
book
- FIALA, J.; MAZAL, P.; KOLEGA, M.:
Cycle induced microstructural changes,
International Journal of Microstructure and Materials Properties, Vol.6, (2011), No.3/4, pp.259-272, ISSN 1741-8410, Inderscience
journal article - other
- MAZAL, P.; PAZDERA, L.; DVOŘÁČEK, J.:
Application of acoustic emission method in contact damage identification,
INTERNATIONAL JOURNAL OF MATERIALS & PRODUCT TECHNOLOGY, Vol.41, (2011), No.1, pp.140-152, ISSN 0268-1900, Inderscience
journal article - other
List of publications at Portal BUT
- VLAŠIC, F.; VOLÁK, J.; NOHÁL, L.; MAZAL, P.; HORT, F.:
Study of Initial Stages of Fatigue Process Using Non-destructive Testing Methods, Trans Tech Publications
journal article in Web of Science
akce: Materials Structure & Micromechanics of Fracture (MSMF-7), Brno, 01.07.2013-03.07.2013
This paper deals with the basic research of cyclic damage during the initial stages of
fatigue process using the non-destructive testing methods. The acoustic emission method was used
for monitoring of the microstructure changes during fatigue loading. The electrical potential
measurements of specimen and microscopic observation were used mainly to detect the first short
cracks and their propagation. The fatigue tests at room temperature were conducted on titanium
alloy and creep-resistant steel specimens under bending and tension loading. The aim of the study
was to compare the acoustic emission signal at different types of loading until fracture and to
analyze in detail the signal changes in initial stages of fatigue process. This analysis was primarily
based on the waveform similarity and division into classes. The results show the high sensitivity of
the acoustic emission technology in the transition from the stage of surface relief evolution to
the stage of crack nucleation and propagation.
- NOHÁL, L.; HORT, F.; DVOŘÁČEK, J.; MAZAL, P.:
An Experimental Investigation of Rolling Contact Fatigue of Steels Using Acoustic Emission Method,
INSIGHT, Vol.55, (2013), No.12, pp.665-669, ISSN 1354-2575, BINDT
journal article - other
Rolling-element bearings are widely used machine components and their failure can result in damage to the whole machine. A bearing failure can be caused by many factors such as improper lubrication, presence of abrasive particles, overloading, moisture, corrosive environment, improper mounting, electrical discharges and material defects. These causes can be eliminated by observance of correct operating conditions, except rolling contact fatigue (RCF). For this reason, the full-scale bearing life tests or material tests for RCF resistance are performed. Various methods of condition monitoring are used to detect damage of these components or specimens in the industry or during testing in laboratories. An analysis of vibrations from tested bearings/specimens is the most widely used method for damage detection and is based on vibration acceleration measurement and its analysis in the time or frequency domain. A more sensitive method for surface damage or subsurface crack detection is the acoustic emission (AE) method. Over the past three decades, the AE based monitoring has developed as a potential tool for rolling bearing diagnostics. This paper is aimed on detection and monitoring of onset and propagation of natural defects of steel specimens using the AE technology. The experiments were carried out under various loading conditions on specimens of case-hardening steel 16MnCr5. The AE signal parameters such as count rate, cumulative count rate and RMS were compared with vibration levels and temperature. In conclusion, the results of this study suggest that the AE monitoring method can be employed as an evaluation tool for rolling contact fatigue testing of material specimens.
- MAZAL, P.; PAZDERA, L.; NOHÁL, L.; TOPOLÁŘ, L.:
Netradiční aplikace metody akustické emise,
ISBN 978-80-214-4629-8, (2012), VUT v Brně
book
The monography describes the contemporary methods of application options in the area of acoustic emission diagnosis of rotating machinery parts, the quality control in the field of welding, construction and selected areas of the biological sciences.
- MAZAL, P.; NOHÁL, L.; ČERNÝ, M.; ČERMÁK, J.:
Measurements of Acoustic Emission in Evaluating of Sap Flow in Trees, INT SOC HORTICULTURAL SCIENCE
journal article in Web of Science
This article deals with measurement techniques of water conducting system in the trees. Water conducting system (including xylem and phloem) indicates its importance for related physiological processes. However, there are still problems how to measure its functioning (which variables and how), especially in the open field (e. g., forests and orchards) in order to get maximum information about it. In this study we focused on a general description of acoustic events measurable in a wide range of their spectrum (acoustic emission method). The first aim was to detect such signals and the second to learn them and gradually analyze in order to better understand the associated processes causing their occurrence and their relations to plant life.
- HORT, F.; MAZAL, P.; VLAŠIC, F.:
Monitoring of Acoustic Emission Signal of Loaded Axial Bearings,
Journal of Materials Science and Engineering A, Vol.2011, (2011), No.5A, pp.717-724, ISSN 1934-8959, David Publishing
journal article - other
The disclosure of initial stadium of contact fatigue of rotating machines is very difficult. At present, some methods which are suitable for diagnosis exist, such as vibration method, shock pulse method, acoustic emission and others. The article describes laboratory tests with axial bearings which are monitored by acoustic emission method. In the article, experimental stands, measuring devices and chosen types of axial bearings are presented. The exploitation of acoustic emission signal for the lifetime evaluation of selected bearings is shown with the characteristics as number of counts, rise time, maximal amplitude or duration of event. The bearing lifetime is separated to three stages and a representative sample in its time and frequency domain for each of them is chosen. Final failures of the bearings are shown too. The paper is focused also on examples of results obtained with continuous AE signal sensing.