prof. Ing. Martin Trunec, Dr. |
| 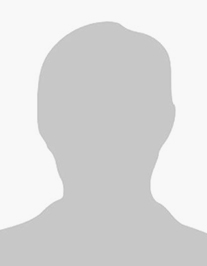 |
Education and academic qualification
- 1988, Ing., Faculty of Mechanical Engineering, BUT, specialization Foundry technology
- 1997, Dr., Faculty of Mechanical Engineering, BUT, specialization Physical and Materials Engineering
- 2006, Assoc. Prof., Faculty of Mechanical Engineering, BUT, specialization Materials Engineering
- 2011, Prof., Faculty of Mechanical Engineering, BUT, specialization Materials Science and Engineering
|
Career overview
- 1988-1990, assistant, Foundry research Brno SVÚM
- 1990-1993, technician, Department of Foundry Engineering FME BUT
- 1993-2006, researcher, Institute of Materials Science and Engineering - Department of Ceramics FME BUT
- 2006-2011, Assoc. Professor, Institute of Materials Science and Engineering - Department of Ceramics and Polymers FME BUT
- 2011-2016, Senior researcher, Central European Institute of Technology, BUT
- since 2011, Professor, Institute of Materials Science and Engineering - Department of Ceramics and Polymers FME BUT
- since 2016, Head of the Advanced ceramic Group, Central European Institute of Technology, BUT
|
Pedagogic activities
- Introduction in Materials Science and Engineering, lectures, 1st year of all specializations FMI BUT
- Technology of non-mettalic materials, lectures and seminars, 3rd year of bachelor study Materials engineering FMI BUT
- Advanced technologies of anorganic materials, selective lectures, PhD. study, FCH BUT
- Supervisor of diploma works in the area of advanced ceramics
- Supervisor of PhD. students in the area of advanced ceramics
|
Scientific activities
- Processing and properties of advanced ceramic materials and nanoceramics
|
Sum of citations (without self-citations) indexed within ISI Web of Knowledge
806
|
Sum of other citations (without self-citations)
15
|
Supervised courses:
Publications:
- TRUNEC, M.; CHLUP, Z.:
Subtractive manufacturing of customized hydroxyapatite scaffolds for bone
regeneration, ELSEVIER SCI LTD, THE BOULEVARD, LANGFORD LANE, KIDLINGTON, OXFORD OX5 1GB, OXON, ENGLAND
journal article in Web of Science
- KAŠTYL, J.; CHLUP, Z.; CLEMENS, F.; TRUNEC, M.:
Mechanical properties of zirconia core-shell rods with porous core and dense shell prepared by thermoplastic co-extrusion
journal article in Web of Science
- TRUNEC, M.; KLIMKE, J.; SHEN, Z.:
Transparent alumina ceramics densified by a combinational approach of spark plasma sintering and hot isostatic pressing, ELSEVIER SCI LTD, THE BOULEVARD, LANGFORD LANE, KIDLINGTON, OXFORD OX5 1GB, OXON, ENGLAND
journal article in Web of Science
- KAŠTYL, J.; CHLUP, Z.; CLEMENS, F.; TRUNEC, M.:
Ceramic core–shell composites with modified mechanical properties prepared by thermoplastic co-extrusion, ELSEVIER SCI LTD
journal article in Web of Science
- TRUNEC, M.; MACA, K.; CHMELÍK, R.:
Polycrystalline alumina ceramics doped with nanoparticles for increased transparency, Elsevier Science Ltd.
journal article in Web of Science
- TRUNEC, M.; MIŠÁK, J.:
Consolidation of nanoparticle suspensions by centrifugation in non-porous moulds, Elsevier Sci. Ltd.
journal article in Web of Science
- TRUNEC, M.; MACA, K.:
Advanced Ceramic Processes,
Advanced Ceramics for Dentistry, pp.123-150, ISBN 978-0-12-394619-5, (2014), Butterworth-Heinemann
book chapter
- TRUNEC, M.; ČÁSTKOVÁ, K.; ROUPCOVÁ, P.:
Effect of Phase Structure on Sintering Behavior of Zirconia Nanopowders, Wiley-Blackwell
journal article in Web of Science
List of publications at Portal BUT
- TRUNEC, M.; ČÁSTKOVÁ, K.; ROUPCOVÁ, P.:
Effect of Phase Structure on Sintering Behavior of Zirconia Nanopowders, Wiley-Blackwell
journal article in Web of Science
Zirconia nanopowder compacts with comparable particle sizes and pore size distributions but different phase structures were prepared. The sintering behavior of monoclinic, tetragonal, and cubic zirconia nanopowders was directly compared. The densification and microstructural changes during sintering were investigated. The tetragonal and cubic nanopowders showed similar sintering behavior whereas the monoclinic nanopowder exhibited a more difficult densification and coarser microstructure compared to tetragonal and cubic powders. The differences in the densification of zirconia nanopowders resulted from significant differences in the microstructure evolution during sintering. The microstructural changes in nanopowder compacts during sintering were described and a correlation between microstructural changes and interfacial energies associated with different crystal structures was discussed.
- BERA, O.; TRUNEC, M.:
Optimization of Fine Alumina Gelcasting Using In Situ Dynamic Rheology, Wiley-Blackwell
journal article in Web of Science
In situ dynamic rheology was used to investigate the polymerization process of gelcasting suspensions based on fine alumina and water solution of methacrylamide and methylene bisacrylamide monomers. Small-strain oscillatory shear measurements were able to detect the progress of the whole gelation process from the liquid suspension to the elastic gel. The parameters describing the gelation kinetics and final gel properties such as idle time, total gelation time and equilibrium complex viscosity were correlated with the initiator/accelerator concentration, linear to cross-linking monomer ratio, polymerization temperature, and alumina loading. A strong catalytic effect of fine alumina particles on the decomposition of ammonium persulfate into free radicals was established. The catalytic activity of alumina powder was controlled by ions adsorbed on the particle surface. The catalytic effect of alumina in the presence of the Dolapix CE 64 dispersant made the polymerization process independent of the accelerator concentration and enabled the gelation of concentrated ceramic suspensions at and below room temperature without any accelerator. The variations of the polymerization process in the range of investigated gel compositions did not affect the particle packing in green bodies and the densities of sintered ceramic bodies were similar.
- TRUNEC, M.; CHLUP, Z.:
Higher fracture toughness of tetragonal zirconia ceramics through nanocrystalline structure, PERGAMON-ELSEVIER SCIENCE LTD
journal article in Web of Science
Fracture toughness of nanocrystalline zirconia ceramic stabilized with 1.5 mol.% Y2O3 was measured and compared with fracture toughness of submicrometer-grained zirconia ceramics stabilized with 3 mol.% Y2O3. It was found that nanocrystalline ceramics demonstrated higher fracture toughness than submicrometer-grained zirconia ceramics with both optimized and common grain sizes. The high fracture toughness of nanocrystalline zirconia was confirmed by two different testing methods: indentation method (15.5 MPa m0.5) and chevron notched beam method (7.9 MPa m0.5).
- TRUNEC, M.; MACA, K.:
Compaction and Pressureless Sintering of Zirconia Nanoparticles,
Journal of the American Ceramic Society, Vol.90, (2007), No.9, pp.2735-2740, ISSN 0002-7820, Blackwell Publishing
journal article - other
Four nanometer-sized zirconia powders stabilized by 3 mol% Y2O3 were used for the preparation of dense bulk ceramics. Ceramic green bodies were prepared by cold isostatic pressing at pressures of 300-1000 MPa. The size of pores in ceramic green bodies and their evolution during sintering were correlated with the characteristics of individual nanopowders and with the sintering behavior of powder compacts. Only homogeneous green bodies with pores of less than 10 nm could be sintered into dense bodies (>99% t.d.) at sufficiently low temperature to keep the grain sizes in a range <100 nm. Powder with uniform particles of 10 nm in size yielded green bodies of required microstructure. These nanoparticle compacts were sintered without pressure to give bodies (diameter 20 mm, thickness 4 mm) with a relative density higher than 99% and a grain size of about 85 nm (as determined by linear intercept method).
- TRUNEC, M.; CIHLÁŘ, J.:
Thermal removal of multicomponent binder from ceramic injection mouldings,
Journal of the European Ceramic Society, Vol.22, (2002), No.13, pp.2231-2241, ISSN 0955-2219, Elsevier Science
journal article - other
Thermal removal of polymer binder containing low-molecular-weight components from ceramic injection mouldings was studied. The effect of the shape and size of bodies on the process of binder removal was examined. Evaporation of low-molecular-weight components represented the most important process at the beginning of binder removal. It was found that a bed of activated carbon speed up removal of low-molecular-weight components. The mechanism of binder removal in a bed of activated carbon was described. Binder redistribution and evolution of porosity in the body during binder removal was investigated. A high rate of binder removal resulted in non-uniform binder distribution in the body. The formation of defects due to non-uniform binder removal was described and requirements for their elimination were proposed.