Ing. Zdeněk Majer, Ph.D. |
| 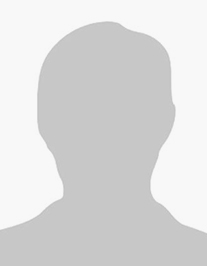 |
Education and academic qualification
- 2009, Ph.D., Faculty of Mechanical Engineering, Brno University of Technology, Applied Sciences in Engineering - Engineering Mechanics
- 2006, Ing., Faculty of Mechanical Engineering, Brno University of Technology, Applied Mechanics - Mechanical Engineering
|
Career overview
- 2009 - to date, assistant professor, Department of Statics and Strength of Material, Institute of Solid Mechanics, Mechatronics and Biomechanics, Faculty of Mechanical Engineering, Brno University of Technology
- 2004 - 2009, research fellow, group of high cycle fatigue, Institute of Physics of Materials (IPM), Academy of Sciences of the Czech Republic
|
Pedagogic activities
- Statics
- Strength of Materials II
|
Scientific activities
- computational mechanics
- fracture mechanics - crack growth
- fracture mechanics - particulate composite
- FEM computing (ANSYS)
|
Projects
- GA ČR P107/10/P503, Multiscale Modeling of Particulate Composites with Mineral Fillers (2010 - 2012, main investigator)
- GA ČR 106/09/H035, Multilevel design of advanced materials (2009, member of research team)
- GA ČR 106/05/H008, Multilevel design of advanced materials (2007 - 2008, member of research team)
|
Sum of citations (without self-citations) indexed within SCOPUS
19
|
Sum of citations (without self-citations) indexed within ISI Web of Knowledge
11
|
Supervised courses:
Publications:
- MAJER, Z.; HUTAŘ, P.; FRANK, A.; ŠEVČÍK, M.; ZOUHAR, M.; PINTER, G.; NÁHLÍK, L.:
Point load effect on the buried polyolefin pipes lifetime, WILEY-BLACKWELL, 111 RIVER ST, HOBOKEN 07030-5774, NJ USA
journal article in Web of Science
- MAJER, Z.; PLETZ, M.; KRAUTGASSER, C.; NÁHLÍK, L.; HUTAŘ, P.; BERMEJO, R.:
Numerical Analysis of Sub-Critical Crack Growth in Particulate Ceramic Composites, ELSEVIER
journal article in Web of Science
- MAJER, Z.; HUTAŘ, P.; NÁHLÍK, J.:
Determination of the Effect of Interphase on Fracture Toughness and the Stiffness of a Polymer Particulate Composite,
MECHANICS OF COMPOSITE MATERIALS, Vol.49, (2013), No.5, pp.1-12, ISSN 0191-5665, Springer
journal article - other
- MARCIÁN, P.; MAJER, Z.; DLOUHÝ, I.; FLORIAN, Z.:
Estimation of Local Mechanical Properties of Highly Porous Ceramic Materials,
Chemické listy, Vol.106, (2012), No.1, pp.476-477, ISSN 0009-2770
journal article - other
- HUTAŘ, P.; MAJER, Z.; NÁHLÍK, L.; ŠESTÁKOVÁ, L.; KNÉSL, Z.:
THE INFLUENCE OF PARTICLE SIZE ON THE FRACTURE TOUGHNESS OF PP-BASED PARTICLE COMPOSITE,
MECHANICS OF COMPOSITE MATERIALS, Vol.45, (2009), No.3, pp.281-286, ISSN 0191-5665, Springer
journal article - other
List of publications at Portal BUT
- MAJER, Z.; HUTAŘ, P.; FRANK, A.; ŠEVČÍK, M.; ZOUHAR, M.; PINTER, G.; NÁHLÍK, L.:
Point load effect on the buried polyolefin pipes lifetime, WILEY-BLACKWELL, 111 RIVER ST, HOBOKEN 07030-5774, NJ USA
journal article in Web of Science
Polymer pipe lifetime is conventionally estimated by internal pressure test. However, important for service are also other types of loading as: additional bending, different type of external loading from sand embedding, or effect of the residual stresses. One of the dangerous type of loading is so-called “point load” caused, for example, by stones in the soil. The present article is focused on the numerical prediction of this effect on the pipe lifetime. For the lifetime estimation of a polymer pipe under point loading, an approach based on combination of numerical calculation and experimental measurements was used. A special numerical algorithm, which optimizes modeled crack front shape according to the real one during simulation of crack propagation, was proposed. Finally, an analytical relationship for the estimation of fracture parameters of propagating crack across the pipe wall crucial for the pipe lifetime estimation is presented in the paper. A significant reduction of the residual lifetime was found for the cracked pipe loaded by additional point load (consideration of indentation effects of stones in the soil) in comparison with pipe loaded by internal pressure only. The approach presented contributes to the safer service of polyolefin pipes.
- MAJER, Z.; PLETZ, M.; KRAUTGASSER, C.; NÁHLÍK, L.; HUTAŘ, P.; BERMEJO, R.:
Numerical Analysis of Sub-Critical Crack Growth in Particulate Ceramic Composites, ELSEVIER
journal article in Web of Science
The strength of glass or ceramic containing materials can be affected by the environment (stress corrosion). Under applied stress, crack-like defects may grow (sub-critically) for stress intensity factors, KI, below the fracture toughness of the material, KIc. The aim of the present work was to develop a two-dimensional finite element model to analyze the subcritical crack growth behavior of ceramic-based particulate composites. The maximum tangential stress criterion (MTS) was used to predict the direction of the crack propagation, in the framework of linear elastic fracture mechanics. The modeled material was a Low Temperature Co-fired Ceramic (LTCC), containing alumina particles embedded in a glass matrix. The experimentally determined SCCG material behavior (i.e. v-KI data) was implemented in the numerical model. The effect of the elastic modulus of the particles on the subcritical crack propagation was investigated. The conclusions of this paper can contribute to a better understanding of the subcritical propagation of cracks in particulate composites.
- MAJER, Z.; HUTAŘ, P.; NÁHLÍK, J.:
Determination of the Effect of Interphase on Fracture Toughness and the Stiffness of a Polymer Particulate Composite,
MECHANICS OF COMPOSITE MATERIALS, Vol.49, (2013), No.5, pp.1-12, ISSN 0191-5665, Springer
journal article - other
The main objective of this paper is the numerical investigation of fracture behavior in polymer particulate composites. In this paper the composite was modeled as a three-phase continuum – the matrix, particles and interphase. Mechanical response was analyzed, as well as the interaction of micro-crack propagation in the matrix filled by rigid particles covered by the interphase. Computations were done for a variety of material properties of the matrix and the interphase using the finite element commercial code ANSYS. It was concluded that specific configurations of the interphase properties can lead to a better understanding of the connection between stiffness and fracture toughness. Linear elastic fracture mechanics was used for the calculations.
- MARCIÁN, P.; MAJER, Z.; DLOUHÝ, I.; FLORIAN, Z.:
Estimation of Local Mechanical Properties of Highly Porous Ceramic Materials,
Chemické listy, Vol.106, (2012), No.1, pp.476-477, ISSN 0009-2770
journal article - other
In this contribution the ceramic foams are studied. The applications of these materials are extensive due to very advantageous combination of properties. This paper is focused on local mechanical properties of individual struts in a highly porous structure. The computational model is created using a micro-CT by a finite element method in ANSYS 12.0 software. The local equivalent stress (HMH criterion) is analyzed depending on struts rotation.
- HUTAŘ, P.; MAJER, Z.; NÁHLÍK, L.; ŠESTÁKOVÁ, L.; KNÉSL, Z.:
THE INFLUENCE OF PARTICLE SIZE ON THE FRACTURE TOUGHNESS OF PP-BASED PARTICLE COMPOSITE,
MECHANICS OF COMPOSITE MATERIALS, Vol.45, (2009), No.3, pp.281-286, ISSN 0191-5665, Springer
journal article - other
The main focus of this paper is the numerical investigation of fracture behaviour in particulate composite (CaCO3 -PP). The composite was modelled as a
three-phase continuum and numerically simulated on a microscopic scale using finite elements. The interaction of micro-crack propagation in the matrix filled by rigid particles covered by the interphase was analyzed. Stress distribution was determined for a variety of particle sizes and material properties of the interphase. The final results, in agreement with the experimental data, confirm the dependence of microcrack behavior on particle size.