doc. Ing. Vladimír Habán, Ph.D. |
| 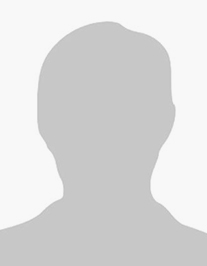 |
Education and academic qualification
- 2001, Ph.D., Brno University of Technology,Faculty of Mechanical Engineering, Mechanical Engineering
- 1994, Ing., Brno University of Technology,Faculty of Mechanical Engineering, Hydraulic and Pneumatics Machines and Equipment
|
Career overview
- 2001- till now assitent lecturer, Brno University of Technology, Faculty
of Mechanical Engineering, Kaplan Department of Fluids Engineering
- 1997-2001 assitent lecturer, Brno University of Technology, Faculty of
Mechanical Engineering, Kaplan Department of Fluids Engineering
|
Pedagogic activities
- present, lecturer for course Dynamic of Power Machines and Their Accessories
- present, lecturer for course Pipeline Engineering
- present, lecturer for course Experiments in Fluid Systems
- supervisor of 26 diploma thesis
|
Sum of citations (without self-citations) indexed within SCOPUS
14
|
Sum of citations (without self-citations) indexed within ISI Web of Knowledge
25
|
Supervised courses:
Publications:
- HIMR, D., HABÁN, V.:
Evaluation of pump characteristic from measurement of fast deceleration,
EFM14 – Experimental Fluid Mechanics 2014 , pp.182-187, (2014), EDP Sciences
conference paper
akce: Experimental Fluid Mechanics 2014, Český Krumlov, 18.11.2014-21.11.2014
- Kozák Jiří, Rudolf Pavel, Sedlář Milan, Habán Vladimír, Hudec Martin, Huzlík Rostislav:
Numerical simulation and experimental visualization of the separated cavitating boundary layer over NACA2412
- HIMR, D., HABÁN, V.:
Damping of Self-Excited Pressure Pulsations in Petrodiesel Pipeline,
Applied Mechanics and Materials, pp.375-282, ISBN 978-3-03835-241-9, (2014), Trans Tech Publications
conference paper
akce: 14th International Scientific and Engineering Conference on Hermetic Sealing, Vibration Reliability and Ecological Safety of Pump and Compressor Machinery, HERVICON+PUMPS 2014, Sumy, 09.09.2014-12.09.2014
- ŠTEFAN, D.; HABÁN, V.; HUDEC, M.; VESELÝ, J.; RUDOLF, P.:
Analysis of Pelton Turbine Jet Decay Using a Proper Orthogonal Decomposition of Experimentally Obtained Image Ensemble,
Book of Abstract, 5th International Workshop on Cavitation and Dynamic Problems in Hydraulic Machinery, (2013), Ecole polytechnique fédérale de Lausanne, Laboratory for Hydraulic Machines
abstract
- HALUZA, M.; POCHYLÝ, F.; HABÁN, V.:
Hydraulic machine with non-uniform cascade,
IOP Conference Series-Earth and Environmental Science, pp.1-7, (2012)
conference paper
akce: 26th IAHR Symposium on Hydraulic Machinery and Systems, Beijing, 19.08.2012-23.08.2012
- Pochylý František, Habán Vladimír, Fialová Simona:
Bulk Viscosity - Constitutive Equations
- HIMR, D.; HABÁN, V.:
Simulation of Low Pressure Water Hammer,
IOP Conference Series-Earth and Environmental Science, pp.1-8, (2010), IOP Publishing Ltd.
conference paper
akce: 25th IAHR Symposium on Hydraulic Machinery and Systems, Timisoara, 20.09.2010-24.09.2010
- HABÁN, V.; RUDOLF, P.; POCHYLÝ, F.; KOUTNÍK, J.; KRÜGER, K.:
Stability of Infinitely Long Asymmetrical Vortex Rope,
Scientific Bulletin of the "Politehnica" University of Timisoara, Vol.52, (2007), No.6, pp.101-108, ISSN 1224-6077, Politechnica University of Timisoare
journal article - other
List of publications at Portal BUT
- HIMR, D., HABÁN, V.:
Evaluation of pump characteristic from measurement of fast deceleration,
EFM14 – Experimental Fluid Mechanics 2014 , pp.182-187, (2014), EDP Sciences
conference paper
akce: Experimental Fluid Mechanics 2014, Český Krumlov, 18.11.2014-21.11.2014
Article describes an experiment where a pump connected to the simple hydraulic circuit is decelerated. Since the deceleration is fast enough the operating point of the machine moves from the initial steady position to the breaking zone, turbine zone and back to the new steady position. A dependence of the specific energy and the torque on the flow rate was evaluated from the measurement of the input and output pressure, torque and rotational speed recorded during the deceleration. Obtained characteristic is much wider than curves obtained from regular measurement of steady state.
- Kozák Jiří, Rudolf Pavel, Sedlář Milan, Habán Vladimír, Hudec Martin, Huzlík Rostislav:
Numerical simulation and experimental visualization of the separated cavitating boundary layer over NACA2412
Cavitation is physical phenomenon of crucial impact on the operation range and service lifetime of the hydraulic machines (pumps, turbines, valves etc.). Experimental measurement of cavitation is expensive and time consuming process, while some important characteristic of the flow are difficult to measure due to the nature of the phenomenon. Current possibilities of computational fluid dynamics provide a way for deeper understanding of cavitation which is important for many applications in the hydraulic machines industry such as expanding operation range or extending lifetime of the hydraulic machines. Simplified model consists of NACA 2412 hydrofoil with 8 degrees angle of attack fixed in between the walls of cavitation tunnel. Present investigation focuses on comparison of vapor volume fractions obtained by 3D CFD simulations and high speed visualization of the real cavitation phenomena. Several operating regimes corresponding to different cavitation numbers are studied with aim to assess the dynamics of the separated cavitating sheets/clouds
- HIMR, D., HABÁN, V.:
Damping of Self-Excited Pressure Pulsations in Petrodiesel Pipeline,
Applied Mechanics and Materials, pp.375-282, ISBN 978-3-03835-241-9, (2014), Trans Tech Publications
conference paper
akce: 14th International Scientific and Engineering Conference on Hermetic Sealing, Vibration Reliability and Ecological Safety of Pump and Compressor Machinery, HERVICON+PUMPS 2014, Sumy, 09.09.2014-12.09.2014
A pumping station in a fuel storage suffered from pressure pulsations in a petrodiesel pipeline. Check valves protecting the station against back flow made a big noise when disc hit a
seat. Due to employees complaints we were asked to solve the problem, which could lead to serious mechanical problems.
Pressure measurement in the pipeline showed great pulsations, which were caused by self-excited oscillation of control valves at the downstream end of pipeline. The operating measurement did not catch it because of too low sampling frequency.
One dimensional numerical model of the whole hydraulic system was carried out. The model consisted of check valve, pipeline and control valve, which could oscillate, so it was possible to simulate the unsteady flow. When the model was validated, a vessel with nitrogen was added to attenuate pressure pulsations.
According to the results of numerical simulation, the vessel was installed on the location. Subsequent measurement proved noticeably lower pulsations and almost no noise.
- ŠTEFAN, D.; HABÁN, V.; HUDEC, M.; VESELÝ, J.; RUDOLF, P.:
Analysis of Pelton Turbine Jet Decay Using a Proper Orthogonal Decomposition of Experimentally Obtained Image Ensemble,
Book of Abstract, 5th International Workshop on Cavitation and Dynamic Problems in Hydraulic Machinery, (2013), Ecole polytechnique fédérale de Lausanne, Laboratory for Hydraulic Machines
abstract
The decay of the jet produced by the Pelton turbine nozzle is analyzed using the proper orthogonal decomposition of image ensemble obtained from a high speed camera. The ensembles of images were recorded with frequency of 1000Hz and frame size 800x600 pixels, where only the part with a boundary between jet and air is considered. The spatio-temporal behavior of the jet decay is carried out for several flow regimes depending on head and nozzle opening. The first comparison is performed for constant nozzle opening and various heads, while the second one for constant head and various nozzle openings. The nozzle was supplied by a centrifugal pump controlled by a frequency convertor. An image processing, proper orthogonal decomposition and graphical representations are performed using a self-written script in MATLAB software. The effort is to extract main unsteady frequencies and assign them to the behavior of the jet decay – longitudinal and transverse fluctuations. Noticeable is redistribution of spatio-temporal shape of modes when the nozzle operating conditions are changed. One of the jet regimes is also influenced by the frequency of centrifugal pump. Presented results of this work show how the potential undesirable frequency of the jet can be determined when the Pelton turbine is operated.
- HALUZA, M.; POCHYLÝ, F.; HABÁN, V.:
Hydraulic machine with non-uniform cascade,
IOP Conference Series-Earth and Environmental Science, pp.1-7, (2012)
conference paper
akce: 26th IAHR Symposium on Hydraulic Machinery and Systems, Beijing, 19.08.2012-23.08.2012
In this article is introduced the sentence of an extension of operational zone of hydraulic machines. The problems of its extending is based on the design of non-uniform cascade. The non-uniform cascade is connected with other factors. The change of own frequency of the runner of a hydraulic machine and pressure pulsations. The suitable construction of non-uniform cascade is introduced on the results of computational simulation and experiment.