prof. Ing. Jindřich Petruška, CSc. |
| 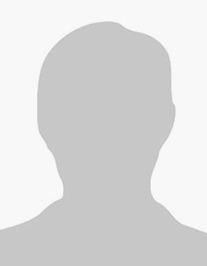 |
Education and academic qualification
- 1981, MSc., Faculty of Mechanical Engineering BUT, specialization Transportation machines
- 1985, PhD., Faculty of Mechanical Engineering BUT, specialization Mechanics of Stiff and Deformable Solids and Continua
- 1995, Assoc.Prof., Faculty of Mechanical Engineering BUT, specialization Mechanics
- 2006, Prof., Faculty of Mechanical Engineering BUT, specialization Applied Mechanics
|
Career overview
- 1981-1984, PhD study, Faculty of Mechanical Engineering, BUT
- 1983, Researcher, Vitkovice Ironworks
- 1984-1985, Research visitor, University of Wales, Swansea, UK
- 1986-1989, Researcher, Inst. of Solid Mechanics, Faculty of Mech.Eng., BUT
- since 1989, Lecturer, Inst. of Solid Mechanics, Mechatronics and Biomechanics, Faculty of Mech.Eng., BUT
|
Pedagogic activities
- Start of teaching activities in 1981 during the PhD study, leading seminars in all basic undergraduate courses of Solid Mechanics
- Lectures in Statics and Strength of Materials
- Introduction of three new courses in the Applied Mechanics curriculum
- Regular member of examining boards, reviews of Master and Doctoral theses
- Tutor of more than 40 Master and 8 Doctoral theses
- Author or co-author of seven lecture notes
|
Scientific activities
- Computational evaluation of strength and reliability of structures by FEM, in recent years concentrated to modelling of nonlinear effects of material, large displacement and contact, as they are manifested in the simulation of forming processes. This activity covered both development of original FE-based software and usage and modification of commercial codes. The results were published in almost one hundred of conference papers, journals and research reports for industrial partners.
- Basic stages:
- 1981-1984, Special FE-based code for inverse problems of elasticity
- 1984-1985, Optimization of structures with respect to plastic behaviour
- 1985-1992, Development of original programs for plastic and contact problems at small deformations
- 1992-1997, Development of programs for forming simulation as a rigid-plastic flow formulation problem
- since 1997, Solution of specific problems of material processing by both commercial and special software (Analysis of ductile fracture criteria, Identification of material parameters, Fast simulation of leveling processess by special software based on Eulerian description of material flow)
|
Academic internships abroad
- 1984-1985, University of Wales, Swansea, UK, researcher
- 1992, Technical University of Rijeka, Croatia, host professor
- 1993, CEMEF Laboratory, Ecole Nationale Superieure des Mines de Paris, Sophia-Antipolis, France, research internship
- 2005, 2006, 2007, University of Malta, Malta, host professor
- 2017, 2018, 2019 University of Malta, visiting external examiner
|
University activities
- 1997-2003, Vice-director of institute
- since 2003, Head of Institute of Solid Mechanics, Mechatronics and Biomechanics
- since 2006, Member of Scientific Board of the Faculty of Mech.Eng., BUT
|
Non-University activities
- since 2003, Chairman of the local branch and member of the Control Board of the Czech Society for Mechanics
- 2008-2010 Chairman of G1 comittee in Universities Development Fund
- 2010-2015 Member of Editorial Board of Engineering Mechanics journal
- since 2012 Member of the IFToMM Czech national commitee
- 2012-2016 Member of the Accreditation Commision of the Czech Republic
- 2016-2018 Member of Board of the National Accreditation Agency for university education
- chairman of the IUTAM National Comittee
|
Industry cooperation
Successful cooperation in projects and contracts from industry, in the last five years especially with the following partners: ABB s.r.o., ŽĎAS a.s., UNIS spol s r.o., Siemens Electric Machines s.r.o., Slovácké strojírny a.s., Honeywell spol. s r.o., Poličské strojírny a.s., COMTES FHT a.s., Ústav aplikované mechaniky Brno s.r.o. and others.
|
Projects
- CZ.1.07/2.2.00/07.0406, Introduction of problem based education to mechanical engineering curricula, 2009-2012
- CZ.1.07.2.4.00.12.0030, Mechanical engineering cooperative network, 2009-2012
- GA101/06/0914, Numerical simulation of large elastoplastic deformation and its application in metal forming processes, 2006-2008
- GA101/09/1630, Numerical solution of stationary and nonstationary disperse waves propagation in mechanical systems, 2009-2013
- MPO ČR č. FR-TI1/185, Mobile scrap metal shears, 2009-2011
- MPO ČR č. FR-TI1/264, Design and realization of a forge manipulator, 2011-2012
- MPO ČR č. FR-TI1/385, Levelling machine for rods and pipes, 2009-2012
- MPO ČR č. FR-TI2/010, New system of doors for transport vehicles, 2010-2012
- MPO ČR č. FR-TI3/441, Development of crankshaft shear press with a new drive, 2011-2012
- TA04020806, Selection and implementation of procedures for low-cycle fatigue evaluating of reactor vessels internals including multiaxial stress states, 2014-2017
- TH03010012, Effective stress relieve of large welded structures, 2018-2021
- FW01010479, Electric drive unit for bus doors, 2020-2022
|
Sum of citations (without self-citations) indexed within SCOPUS
280
|
Sum of citations (without self-citations) indexed within ISI Web of Knowledge
240
|
Supervised courses:
Publications:
- ŠEBEK, F.; PETRUŠKA, J.; KUBÍK, P.:
Lode dependent plasticity coupled with nonlinear damage accumulation for ductile fracture of aluminium alloy
journal article in Web of Science
- JENÍK, I.; KUBÍK, P.; ŠEBEK, F.; HŮLKA, J.; PETRUŠKA, J.:
Sequential simulation and neural network in the stress–strain curve identification over the large strains using tensile test
journal article in Web of Science
- ŠEBEK, F.; KUBÍK, P.; PETRUŠKA, J.; HŮLKA, J.:
Extremely Low-Stress Triaxiality Tests in Calibration of Fracture Models in Metal-Cutting Simulation
journal article in Web of Science
- PETRUŠKA, J.; NÁVRAT, T.; ŠEBEK, F.:
Novel approach to computational simulation of cross roll straightening of bars
journal article in Web of Science
- ŠEBEK, F.; KUBÍK, P.; HŮLKA, J.; PETRUŠKA, J.:
Strain hardening exponent role in phenomenological ductile fracture criteria
journal article in Web of Science
- KUBÍK, P.; ŠEBEK, F.; HŮLKA, J.; PETRUŠKA, J.:
Calibration of ductile fracture criteria at negative stress triaxiality
journal article in Web of Science
- ŠEBEK, F.; KUBÍK, P.; PETRUŠKA, J.:
Prediction of central bursting in the process of forward extrusion using the uncoupled ductile failure models
journal article in Scopus
- ŠEBEK, F.; KUBÍK, P.; PETRUŠKA, J.:
Chevron crack prediction using the extremely low stress triaxiality test
journal article in Scopus
- ŠEBEK, F.; PETRUŠKA, J.; NÁVRAT, T.:
Euler-type algorithm applied to leveling process analysis,
Engineering Mechanics, Vol.21, (2014), No.3, pp.185-191, ISSN 1802-1484
journal article - other
- PETRUŠKA, J.; KUBÍK, P.; HŮLKA, J.; ŠEBEK, F.:
Ductile Fracture Criteria in Prediction of Chevron Cracks,
Advanced Materials Research, Vol.716, (2013), No.1, pp.653-658, ISSN 1022-6680, Trans Tech Publications
journal article - other
- PETRUŠKA, J.; KUBÍK, P.; HŮLKA, J.:
Computational Simulation of Small Punch Test,
Applied Mechanics and Materials, Vol.232, (2012), No.1, pp.497-501, ISSN 1660-9336, Trans Tech Publications
journal article - other
- PETRUŠKA, J.; NÁVRAT, T.; ŠEBEK, F.:
A New Model for Fast Analysis of Leveling Process,
Advanced Materials Research, Vol.586, (2012), No.1, pp.389-393, ISSN 1022-6680, Trans Tech Publications
journal article - other
List of publications at Portal BUT
- ŠEBEK, F.; KUBÍK, P.; HŮLKA, J.; PETRUŠKA, J.:
Strain hardening exponent role in phenomenological ductile fracture criteria
journal article in Web of Science
The performance of ductile fracture criteria often depends on the accuracy of material constants identification. Calibration process of three uncoupled phenomenological models was analysed. All of them contain the strain hardening exponent which is related to material plasticity as one of the fracture criteria parameter. More flexibility, better approximation of the fracture locus and more convenient shape of the fracture envelope might be reached when the strain hardening exponent is considered as another independent parameter of the fracture criteria in the identification process. Results are illustrated on the example of two structural steels, AISI 316L and AISI 1045, respectively.
- ŠEBEK, F.; PETRUŠKA, J.; NÁVRAT, T.:
Euler-type algorithm applied to leveling process analysis,
Engineering Mechanics, Vol.21, (2014), No.3, pp.185-191, ISSN 1802-1484
journal article - other
Presented paper is focused on description of algorithm for fast analysis of leveling process in detail and on verification of obtained results. The main idea is based on using Finite Element Method (FEM) and solving its fundamental equation. The algorithm is programmed using software MATLAB. The program has modular structure, so it is not complicated to modify any setting or utility. Leveling process of long semi products respecting the Eulerian approach is considered. Curved material passes through laterally offset rollers so repeated elasto-plastic bending occurs. Plastic deformation causes redistribution of residual stress. The semi product is straightened when rollers are appropriately positioned. Given problem is complicated due to high inherent nonlinearity and sensitivity, caused by cyclic plasticity. Useful setting of the leveling machine is found by iterative process, based on input measured geometrical data and material characteristics.
- PETRUŠKA, J.; NÁVRAT, T.; ŠEBEK, F.:
A New Model for Fast Analysis of Leveling Process,
Advanced Materials Research, Vol.586, (2012), No.1, pp.389-393, ISSN 1022-6680, Trans Tech Publications
journal article - other
The paper deals with numerical analysis of the process of roller leveling of long products. The problem of multiple elastic plastic bending is solved by a program in Matlab, which is based on the Finite Element Method. The aim is to provide a simple, user friendly tool, capable of quick and reliable analysis of the process without the necessity to work with large multipurpose FEM packages. Direct solution of the problem is formulated, starting from the roll intermeshing and product geometry. Roller loading, product deflection, curvature and plastification are the output parameters of the program. With fast and reliable solution of the direct problem, optimal setting of the leveling process will be sought in an iterative process.
- PETRUŠKA, J., JANÍČEK, L.:
On the evaluation of strain inhomogeneity by hardness measurement of formed products,
Journal of Materials Processing Technology, Vol.143-144, (2003), No.12, pp.300-305, ISSN 0924-0136
journal article - other
Large plastic deformation of cold formed metal is followed by its hardening, which can be experimentally evaluated by measuring
hardness. To convert the measured hardness values into strain, the strain–hardness reference curves are used. Their evaluation is traditionally
based on compression tests of cylindrical specimens. New procedure of reference curves evaluation is suggested here, based on an FE
simulation of a forming process and direct relation of computed strain and measured hardness. The procedure is illustrated on the example
of forward extrusion process and reference curves, obtained by classical and newly suggested procedure are compared.
- RUSZ, S., PETRUŠKA, J., JANÍČEK, L.:
Computationally-experimental workability determination of compressed cylindrical specimen with surface defect,
Journal of Materials Processing Technology, Vol.80-81, (1998), pp.572-578, ISSN 0924-0136
journal article - other
Fracture of cylindrical specimens with longitudinal surface notch under compression test were experimentally studied. Geometry of the specimens (height to diameter ratio, notch depth) and frictional conditions (grooved, dry smooth and lubricated smooth platens) were changed. Subsequent finite element numerical simulation of the tests produced local stress-strain history at the notch tip. This was used for evaluation of the ability of various ductile facture criteria to predict correctly the fracture initiation. Results for individual criteria are presented and discussed in the paper.